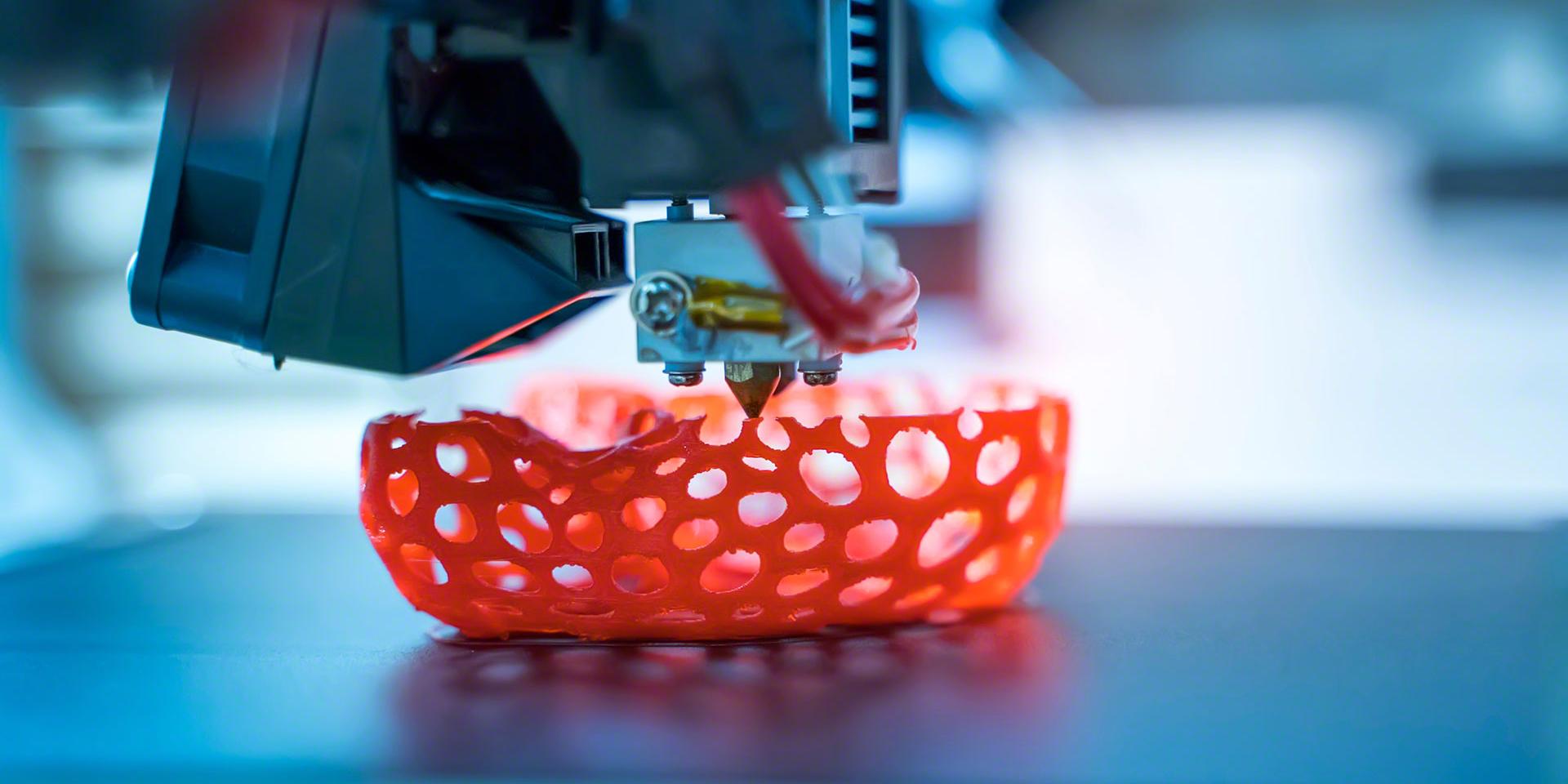
Additive manufacturing represents an approach to creating three-dimensional objects. Unlike traditional methods, such as CNC machining that remove material, this innovative process builds items layer by layer, directly from a digital design in CAD software. This capability has opened up possibilities for design, customization, and efficient production across a myriad of industries.
What is Additive Manufacturing?
Additive manufacturing, commonly known as 3D printing, fundamentally redefines how products are made by constructing objects through the successive addition of material. This starkly contrasts with conventional “subtractive” methods, which typically involve carving, machining, or removing material from a larger block.
At its core, additive manufacturing relies on a few basic elements that enable its unique capabilities:
- Digital Model: Every AM process begins with a 3D digital design, usually created using Computer-Aided Design (CAD) software or by 3D scanning an existing object.
- Material: A wide array of materials can be used, including various polymers, metals, ceramics, composites, and even biomaterials.
- Layer-by-Layer Fabrication: The defining characteristic is the sequential deposition and bonding of material, layer upon layer, until the final three-dimensional object is complete.
- Custom Option: The inherent layer-by-layer nature allows for unparalleled customization, enabling the creation of unique, tailor-made products for individual needs without incurring significant additional costs.
The role of additive manufacturing is rapidly expanding, from facilitating rapid product development and customized production to enabling on-demand manufacturing and localized supply chains. It’s a transformative technology that empowers businesses, including many 3D printing companies, to innovate at an accelerated pace and explore design complexities previously unattainable.
How Additive Manufacturing Works?
Additive manufacturing brings digital designs to life by precisely adding material in successive layers, guided by a 3D computer model. This digital blueprint acts as the precise instructions, dictating the exact shape and dimensions of each subsequent layer. As the layers fuse together, they gradually build up the desired three-dimensional object, transforming a virtual concept into a tangible reality.
The basic Process:
The journey of additive manufacturing typically involves several distinct steps to bring a digital design into physical existence:
- A 3D model is designed using CAD software or by scanning an object.
- Convert the model to a standard file format, typically STL.
- This 3d model is then sliced into thin layers by specialized software.
- The machine is prepared with the proper 3d printing material (plastic or metal).
- Build the object layer by layer, directly on the 3d print bed.
- The finished part is carefully removed from the build platform.
- The completed object then undergoes necessary post-processing steps.
Materials for Additive Manufacturing

Img: different types of 3d printing materials
The diverse range of materials capable of being transformed through additive manufacturing is a key driver of its widespread adoption and innovative applications. This extensive range, from flexible polymers to robust metals, directly impacts an object’s final properties and suitability for specific uses.
Such a versatile palette enables the creation of components with tailored characteristics and structural integrity. Here are some commonly used materials, categorized by their type:
Plastics:
- PLA (Polylactic Acid): A popular, biodegradable plastic, known for ease of use and ideal for general prototyping.
- ABS (Acrylonitrile Butadiene Styrene): A durable, impact-resistant thermoplastic widely used for functional parts.
- Nylon (Polyamide): Valued for its strength, flexibility, and chemical resistance, suitable for engineering applications.
- TPU (Thermoplastic Polyurethane): Offers excellent elasticity and abrasion resistance, perfect for flexible components.
- Resins (Photopolymers): Liquid materials cured by light, commonly used for high-detail parts with smooth finishes.
Metals:
- Stainless Steel (e.g., 316L): A versatile alloy known for its high strength and corrosion resistance across various industries.
- Titanium Alloys (e.g., Ti6Al4V): Exceptional for their high strength-to-weight ratio and biocompatibility, critical in aerospace and medical fields.
- Aluminum Alloys (e.g., AlSi10Mg): Lightweight and possessing good thermal properties, frequently used in automotive and aerospace.
- Nickel Alloys (e.g., Inconel 718): Renowned for maintaining strength at high temperatures and excellent corrosion resistance in extreme environments.
- Tool Steels (e.g., Maraging Steel 300): Offer high hardness and wear resistance, making them ideal for durable tools and inserts.
Different Types of Additive Manufacturing
Far from a single technique, additive manufacturing is a vast landscape of processes, each with its own way of building and specific material strengths. Navigating these diverse methods is key to choosing the ideal approach and truly unlocking the technology’s impressive capabilities.
Stereolithography apparatus (SLA)
Stereolithography (SLA) is one of the earliest and most precise forms of additive manufacturing, utilizing a liquid photopolymer resin and an ultraviolet (UV) laser. The laser precisely cures and solidifies layers of the resin, one by one, to form highly detailed and smooth-surfaced objects.
This method is particularly valued for producing prototypes, master patterns for molding, and intricate parts requiring high aesthetic quality and accuracy.
Fused-deposition modeling (FDM)
Fused Deposition Modeling (FDM) is perhaps the most widely recognized and accessible form of 3D printing, operating by extruding a thermoplastic filament through a heated nozzle. This melted material is then deposited layer by layer onto a build plate, solidifying as it cools to construct the desired object.
FDM is particularly favored for its affordability, versatility, and suitability for rapid prototyping and producing functional parts, making it a staple for hobbyists and professionals alike.
Binder Jetting
Binder jetting is an additive manufacturing process that builds objects layer by layer by using a liquid binding agent to selectively join powdered material. A print head deposits tiny droplets of the binder onto a thin layer of powder, solidifying it to form a cross-section of the part.
This method is particularly notable for its ability to produce complex geometries without the need for support structures, making it versatile for a wide range of materials, including metals, sands, and ceramics, which often undergo post-processing like sintering or infiltration for final strength.
Powder Bed Fusion (PBF)
Powder Bed Fusion (PBF) is a foundational group of additive manufacturing processes that create objects by selectively fusing powdered material, layer by layer, within a heated build chamber. These methods precisely apply a high-energy source, such as lasers or electron beams, to melt or sinter specific areas of the powder bed according to the digital design. Some PBF techniques include:
- Selective Laser Sintering (SLS)
- Selective Laser Melting (SLM)
- Selective Heat Sintering (SHS)
- Electron Beam Melting (EBM)
- Direct Metal Laser Sintering (DMLS)
- Direct Metal Laser Melting (DMLM)
This broad array of PBF technologies is collectively best suited for manufacturing complex, high-performance components with intricate geometries, particularly in aerospace, medical, and automotive sectors.
Material Jetting (MJ)
Material Jetting (MJ) operates much like a traditional 2D inkjet printer, but instead of ink on paper, it precisely jets tiny droplets of photopolymer or wax materials onto a build platform. These droplets are then immediately cured by a UV light source, solidifying layer by layer to form the object.
This method stands out for its exceptional detail, smooth surface finishes, and the unique ability to print with multiple materials and colors simultaneously within a single build. Material Jetting is therefore best suited for highly detailed prototypes, realistic models, and parts requiring multi-material functionality or vibrant aesthetics.
Direct Energy Deposition (DED)
Direct Energy Deposition (DED) is an additive manufacturing process that builds objects by feeding wire or powder material into a melt pool created by a focused energy source, such as a laser, electron beam, or plasma arc. As the material melts and solidifies, it fuses onto a substrate, layer by layer, allowing for the creation of new parts or the repair of existing components.
This robust method is particularly well-suited for building and repairing large-scale metal parts, applying protective coatings, and fabricating objects with functionally graded materials.
Additive Manufacturing: Pros and Cons
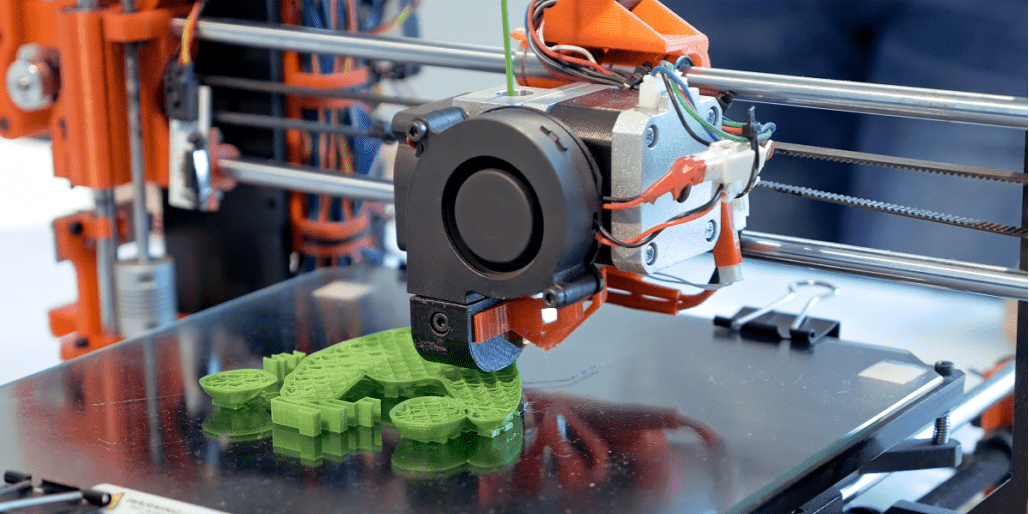
Now we’ll pivot to understanding the practical advantages and disadvantages of additive manufacturing. Like any powerful technology, it presents a compelling set of benefits while also carrying certain limitations that inform its most effective applications.
Exploring both sides helps to paint a complete picture of its current role and future potential in modern manufacturing. Here’s a breakdown of the key pros and cons:
Advantages (Pros) | Disadvantages (Cons) |
Design Freedom & Complexity: Enables creation of intricate geometries, lightweight lattice structures, and consolidated parts impossible with traditional methods. | High Initial Cost: Industrial-grade printers and specialized materials often require significant upfront investment. |
Rapid Prototyping & Iteration: Drastically reduces lead times for creating prototypes, allowing for faster design cycles and product development. | Slower Production Speed (for high volume): While fast for prototypes and small batches, AM can be slower than traditional methods for mass production. |
Customization & Personalization: Facilitates cost-effective production of unique, tailored products for individual needs, like medical implants. | Limited Material Selection (compared to traditional): Although expanding, the range of AM-compatible materials is still smaller than conventional manufacturing. |
Reduced Material Waste: Builds objects layer by layer, minimizing scrap material compared to subtractive manufacturing. | Post-Processing Requirements: Most AM parts require additional steps like support removal, curing, cleaning, or surface finishing. |
Supply Chain Optimization: Allows for on-demand, localized production, reducing inventory needs and mitigating supply chain disruptions. | Part Size Limitations: The build volume of most printers restricts the maximum size of a single printed part, though larger objects can be assembled. |
Low-Volume Production & Tooling Cost Savings: Eliminates the need for expensive tooling or molds, making small production runs economically viable. | Surface Finish & Accuracy: Can sometimes result in visible layer lines or require post-processing to achieve desired surface quality and dimensional accuracy. |
Part Consolidation: Complex assemblies often can be redesigned and printed as a single, integrated component, reducing assembly time and potential failure points. | Skills Gap: Requires specialized knowledge in design for additive manufacturing, material science, and machine operation. |
The Ecosystem of Additive Manufacturing
Additive manufacturing is not merely a collection of machines but a sophisticated ecosystem. Each component plays a vital role, from the initial digital design to the final perfected product, ensuring the seamless flow of innovation.
- CAD Software: This is the brain of the operation, where initial ideas take form as intricate 3D digital designs, dictating every detail of the final part.
- Other Software: Specialized programs for slicing, simulation, and workflow management act as the nervous system, translating designs into machine instructions and optimizing the printing process.
- 3D Models: The digital blueprint serves as the DNA of the object, containing all the information needed for its precise layer-by-layer construction.
- Materials: These are the building blocks, the raw ingredients that give the final product its physical properties, ranging from flexible plastics to robust metals.
- 3D Printing Machines: Often considered the hands of the operation, these advanced machines are the physical enablers that precisely deposit and fuse materials to build the object.
- Post-Processing: This critical final stage is akin to finishing touches, refining the printed part’s surface, strength, and accuracy to meet specific functional and aesthetic requirements.
- Custom Demands: These user-specific needs and unique requirements are the driving force, continually met and optimized by advanced 3D printing services like those offered by us – Xmake.
Applications of Additive Manufacturing
Additive manufacturing has moved far beyond simple prototyping, now transforming various industries by enabling unprecedented design freedom, customization, and efficiency. Its ability to create complex geometries and functional parts on demand has unlocked innovative solutions across a wide spectrum of applications.
Aerospace & Defense
Additive manufacturing is changing the aerospace and defense sectors by enabling the production of lighter, stronger, and more complex components with integrated functionalities. This leads to significant fuel savings, enhanced performance, and simplified assembly for critical systems. Custom Parts Examples:
- Lightweighting brackets and structural components for aircraft.
- Fuel nozzles with optimized internal geometries for improved efficiency.
- Ducting systems and cabin interior parts for weight reduction.
- Satellite components and propulsion system parts for space applications.
Medical & Dental
The medical and dental fields are profoundly impacted by additive manufacturing’s capacity for mass customization and patient-specific solutions. It allows for the creation of perfectly fitted devices that improve patient outcomes and streamline surgical procedures. Custom parts examples:
- Patient-specific surgical guides for precise operations.
- Custom dental crowns, bridges, and clear aligner models (e.g., Invisalign).
- Orthopedic implants, such as hip and knee replacements, tailored to individual anatomy.
- Prosthetics and orthotics that offer a perfect, comfortable fit for users.
Automotive
In the automotive industry, additive manufacturing accelerates design cycles, enables lightweighting, and facilitates the production of custom and low-volume parts. It supports everything from rapid prototyping to specialized end-use components for high-performance vehicles. Custom parts examples:
- Lightweight engine components and manifold designs for performance cars.
- Custom interior elements like dashboard trims, air vents, and personalized shift knobs.
- Obsolete or classic car spare parts produced on demand.
Consumer Goods & Electronics
Additive manufacturing empowers the consumer goods and electronics sectors to offer highly personalized products and bring innovative designs to market faster. It supports rapid iteration and mass customization, catering to evolving consumer preferences. Custom parts examples:
- Custom eyewear frames tailored to individual facial measurements.
- High-performance athletic footwear midsoles with optimized lattice structures (e.g., Adidas 4DFWD).
- Personalized phone cases and electronic housings.
- Intricate jewelry designs and unique fashion accessories.
Tooling, Jigs & Fixtures
Additive manufacturing provides a cost-effective and agile solution for creating custom tooling, jigs, and fixtures used in various manufacturing processes. This enables faster production line setup, improved ergonomics, and significant cost savings compared to traditional machining. Custom parts examples:
- Assembly jigs and fixtures for precise part alignment.
- Custom molds and patterns for low-volume injection molding or casting.
- Ergonomic tools for specific worker comfort and efficiency.
- Robot end-effectors and grippers designed for unique part handling.
The industries detailed above showcase just a fraction of additive manufacturing’s transformative impact. Others, including those in new energy, construction, and even fashion, are leveraging its unique capabilities for specialized components. This widespread adoption underscores AM’s versatility and its growing role as a crucial tool for innovation across the global manufacturing landscape.
Become a Partner with Xmake
Additive manufacturing is fundamentally reshaping industries, offering unprecedented design freedom and customization. As the technology matures, its ongoing advancements in quality, standardization, and sustainability will continue to drive innovation.
Collaborate with Xmake for your CNC machining, 3D printing, and rapid prototyping needs. Get an instant online quote to launch your next project today!
Frequently Asked Questions
1. How much does additive manufacturing cost?
Ah, the million-dollar question – or sometimes, the ten-dollar question! The cost of additive manufacturing is a bit like ordering coffee: it varies wildly based on the “blend” (material), the “size” (part geometry and volume), and how “fancy” you want it (post-processing). For prototypes or highly complex, low-volume parts, it can be surprisingly cost-effective, often saving you tooling costs. But if you’re looking to print a million simple widgets, traditional methods might still win the price race… for now!
2. Is CNC additive manufacturing?
That’s like asking if painting is sculpting! CNC (Computer Numerical Control) machining is the proud patriarch of subtractive manufacturing. It works by precisely removing material from a solid block, carving out the desired shape.
Additive manufacturing, conversely, is all about adding material layer by layer. Think of CNC as a master sculptor chipping away marble, while additive manufacturing is a meticulous builder assembling bricks. Both brilliant, just different philosophies!
3. What is the ASTM definition of additive manufacturing?
According to the ISO/ASTM 52900 standard, additive manufacturing (AM) is defined as “the process of joining materials to make parts from 3D model data, usually layer upon layer, as opposed to subtractive and formative manufacturing methodologies.”
4. How does Additive manufacturing support real-world projects?
Additive manufacturing is the go-to for creating rapid prototypes for immediate testing, crafting custom medical implants, or producing lightweight, complex components for rockets that defy gravity. Essentially, if you can dream it in a 3D model, AM is often the fastest, most efficient way to get a physical version into your hands, making “impossible” projects just another Tuesday.