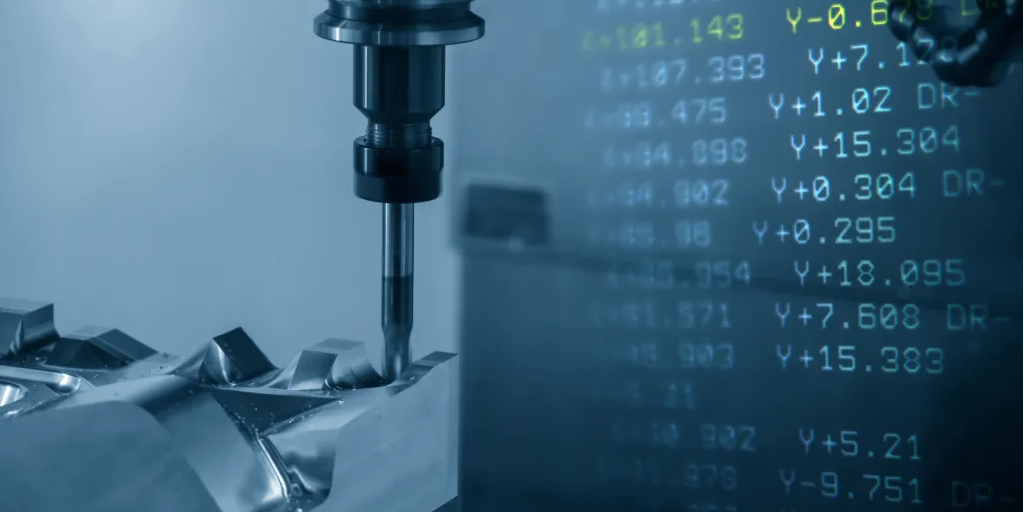
Understanding the relationship between speed, feed, and material properties is essential to achieving optimal performance. One of the most important but sometimes overlooked parameters is Surface Feet per Minute (SFM), which directly influences tool life, surface finish, and overall efficiency.
While it may sound technical, SFM is simply a measure of how fast the cutting tool moves across the material surface. In this article, we’ll break down what SFM means, why it matters, and how to calculate it effectively.
What Is SFM?
SFM is a fundamental concept in machining that defines the speed at which the cutting edge of a tool moves across the surface of the material being machined. It is a critical factor that influences machining efficiency, surface finish, heat generation, and tool longevity.
Properly understanding and applying SFM ensures that the cutting process remains stable and effective across different materials and tooling conditions.
SFM Meaning in Machining

SFM, or Surface Feet per Minute, represents the linear speed of the cutting tool in contact with the workpiece. It is expressed in feet per minute (ft/min) and is calculated based on the rotational speed of the tool or workpiece and the diameter at the point of contact.
In practical terms, SFM tells us how many feet of material the tool will contact in one minute at the given spindle speed. This metric helps machinists determine how fast they can cut a specific material without causing excessive tool wear or surface damage.
The Units of SFM
SFM is measured in feet per minute (ft/min), which quantifies the linear distance the cutting tool travels along the surface of the material every minute. This unit reflects the actual speed at which the tool engages the workpiece, not just how fast it spins. For example, if a tool is rotating around a small-diameter part, the surface speed will be relatively low, even at high RPM.
On the other hand, a larger diameter at the same RPM will result in a much higher surface speed. This distinction highlights why SFM provides a more accurate and meaningful measure of cutting conditions than rotational speed alone.
In metric contexts, this value is often converted to meters per minute (m/min) using the following formula below, but the principle remains the same:
Speed (m/min) = SFM × 0.3048
-
- 1 foot = 0.3048 meters
- Since SFM is in feet per minute, multiplying by 0.3048 gives you the equivalent speed in meters per minute.
If you’re cutting at 200 SFM, then:
200 SFM × 0.3048 = 60.96 m/min
This conversion is especially useful when using European or international tooling standards, which typically specify cutting speeds in metric units.
Understanding the units is crucial for setting proper speeds and feeds, especially when working with data sheets or tooling guidelines that specify recommended SFM values.
Why SFM Matters in Machining?
Applying the correct SFM ensures that the cutting tool operates within its optimal performance range. If SFM is too low, it can lead to poor surface finishes and inefficient material removal. Conversely, an excessively high SFM generates excess heat, accelerating tool wear and potentially damaging the workpiece.
Manufacturers often provide recommended SFM values for different materials and tool types, allowing machinists to fine-tune their settings for consistent and cost-effective results. In high-precision or high-volume environments, SFM becomes a strategic factor in balancing productivity with quality and tool life.
SFM vs. RPM: What’s the Difference?
RPM, or Revolutions Per Minute, is a measure of how many times a rotating object, such as a cutting tool or workpiece, completes a full 360-degree rotation in one minute.
While RPM is a direct indicator of rotational speed, it does not consider the diameter of the tool or the surface distance being covered. This is where SFM provides additional context. SFM translates rotational speed into linear speed at the cutting surface, which is far more relevant in machining, as it reflects how fast the tool is engaging the material. In contrast, RPM remains constant for a given spindle speed, regardless of diameter, but the effective cutting speed (SFM) can vary significantly with diameter changes.
This distinction is crucial when switching between tools of different diameters or working with different materials, as using the same RPM may result in vastly different surface speeds. Overlooking this can lead to improper cutting conditions—either too slow, causing inefficient machining, or too fast, leading to overheating and premature tool failure. Here is a comparison table on SFM vs RPM:
Aspect | SFM (Surface Feet per Minute) | RPM (Revolutions Per Minute) |
Definition | Linear speed at the material surface | Rotational speed of the tool or part |
Units | Feet per minute (ft/min) | Revolutions per minute |
Dependent On Diameter | Yes | No |
Used For | Determining appropriate cutting speed | Machine spindle setting |
Formula | SFM = (π × Diameter × RPM) / 12 | RPM = (SFM × 12) / (π × Diameter) |
Application | Optimizing tool life, surface finish | Initial machine configuration |
Material Sensitivity | Adjusted based on material being cut | Not directly sensitive to material |
In practice, machinists often start by identifying the correct SFM based on the material and tooling, then calculate the required RPM accordingly. This ensures that the tool operates within optimal conditions for both performance and longevity.
How to Calculate SFM in Machining?
Calculating Surface Feet per Minute (SFM) is a fundamental step in setting up your machining parameters correctly. It allows you to determine how fast the cutting tool should move across the material’s surface based on its diameter and rotational speed. Using the correct SFM is essential for maintaining tool life, achieving the desired surface finish, and ensuring safe and efficient machining.
The Standard SFM Formula
The general formula used in both milling and turning operations is:
SFM = (π × Diameter (inches) × RPM)/12
Let’s break this down:
- SFM – Surface Feet per Minute: the linear speed of the tool at the point of contact with the material.
- π (Pi) – Approximately 3.1416; used to calculate the circumference of a circle.
- Diameter – The outer diameter of the rotating part (e.g., a tool or workpiece), measured in inches.
- RPM – Revolutions Per Minute: how fast the tool or workpiece is rotating.
- 12 – This factor converts inches to feet, since SFM is expressed in feet per minute.
Example Calculation
Let’s say you’re using a 2-inch diameter tool spinning at 1,200 RPM. The SFM would be:
SFM = (3.1416×2×1200)/12 = 7539.84/12 =628.32 ft/min
So, your cutting speed is approximately 628 feet per minute. This number can then be compared with manufacturer recommendations based on the material being machined.
SFM Calculator
SFM in CNC Milling and Turning
While the concept of Surface Feet per Minute (SFM) applies broadly across machining operations, its application differs slightly between CNC milling and CNC turning due to the nature of tool and workpiece movement.
SFM in CNC Milling
In CNC milling, the cutting tool rotates while the workpiece remains stationary or moves linearly along the X, Y, or Z axes. SFM is calculated based on the diameter of the rotating tool and the spindle speed (RPM).
Formula:
SFM = (π × Tool Diameter (inches) × RPM)/12
-
- Larger tool diameters generate higher surface speeds at the same RPM.
- SFM guides the machinist in selecting the proper spindle speed to match material requirements.
For example, cutting aluminum at high speeds may require SFM values exceeding 600 ft/min, while harder materials like stainless steel might require values below 150 ft/min to prevent tool overheating or premature wear.
SFM in CNC Turning
In turning operations, the workpiece rotates, and the cutting tool remains stationary (except for linear feed movement). Here, SFM is determined based on the diameter of the rotating workpiece at the point of contact and the RPM.
Formula:
SFM = ( π × Workpiece Diameter (inches) × RPM)/12
-
- As turning tools cut along the diameter of a spinning workpiece, the SFM changes depending on the cutting depth.
- For external turning, the surface speed is highest at the outer diameter and decreases as the tool moves toward the center (smaller diameter).
- Therefore, constant surface speed (CSS) mode is often used in CNC lathes, where the machine automatically adjusts RPM to maintain a consistent SFM as the diameter changes.
SFM in Milling vs Turning: Differences
Aspect | CNC Milling | CNC Turning |
Rotating component | Tool | Workpiece |
Diameter used in SFM | Tool diameter | Workpiece diameter |
SFM change during cut | Constant (unless tool size changes) | Variable (if cutting at different diameters) |
Typical application | Slotting, facing, contouring | External/internal turning, facing |
Control mode (advanced) | Manual or fixed RPM | Often uses Constant Surface Speed (CSS) |
By tailoring SFM values to the specific operation—milling or turning—machinists can achieve higher efficiency, reduce tool wear, and ensure a more predictable cutting environment, especially in high-precision or production-scale CNC machining.
Other Speed and Feed Terms in Machining
A well-optimized machining process requires more than just understanding SFM. Several other parameters directly influence cutting performance, tool life, and surface finish.
IPT (Inches Per Tooth)
IPT refers to the amount of material a single cutting edge removes per revolution. It is primarily used in milling operations where tools have multiple flutes or teeth. Calculated as feed rate divided by the product of RPM and number of teeth, IPT helps determine whether each tooth is engaging the material efficiently.
Correct IPT selection avoids underfeeding (which reduces productivity) or overfeeding (which risks tool damage).
IPR (Inches Per Revolution)
IPR measures the distance the tool advances during one full revolution of the spindle. It is commonly used in turning, drilling, and boring operations where the feed is applied per revolution rather than per tooth. IPR directly affects chip load, surface finish, and machining stability, making it a key setting for consistent material removal.
DOC (Depth of Cut)
Depth of Cut (DOC) refers to how deep the tool cuts into the material in a single pass, typically measured perpendicular to the surface being machined. In milling, it’s the vertical distance the tool plunges into the material, while in turning, it’s the radial engagement.
Higher DOC values remove more material but increase cutting force, which can lead to tool deflection or chatter if not properly supported.
WOC (Width of Cut)
Width of Cut (WOC), sometimes called radial depth, is the measure of how wide the tool engages with the material during cutting. In milling, it’s the portion of the cutter that is actively removing material in the radial direction.
A smaller WOC is used for finishing passes to reduce stress and improve accuracy, while a larger WOC is chosen for roughing operations to maximize material removal rate.
Conclusion
Understanding what SFM means in machining and how it relates to other essential parameters like IPT, IPR, DOC, and WOC, is fundamental to optimizing any CNC operation.
By using the right formulas and tools, such as an SFM calculator, machinists can make data-driven decisions that enhance both efficiency and precision on the shop floor.
Xmake offers precision CNC services, delivering high-quality machining solutions tailored to your specific needs.
Frequently Asked Questions
1. What’s the difference between SFM and RPM?
While both SFM and RPM (Revolutions Per Minute) describe motion, they measure different aspects. RPM is the number of full revolutions a tool or workpiece makes in one minute, whereas SFM accounts for the cutting speed along the material’s surface.
2. What is SFM in engineering?
In engineering, SFM (Surface Feet per Minute) is a unit that measures the linear speed at which a cutting tool engages the surface of a material, helping define appropriate machining parameters.
3. What is SFM cutting speed?
SFM cutting speed refers to how fast the cutting edge of a tool moves across the material's surface, typically used to determine the optimal spindle speed for machining operations.